
My first impression of the XL was that I was surprised at how small it was. I like to keep my stiles long for extra clamping space, and so I don’t have to fuss around keeping them perfectly flush. It’s easy to cut the tails off with a tracksaw after the glue-up dries. So, keep that MFT table setup until you finish the glue-up. More than likely you will have to ‘tune up’ a rail or two to get all the joints tight. Test your assembly before glue up-including your clamps. If you don’t round over the tenons a little, it’s nearly impossible to get everything together when you’re gluing up. Honestly, this wasn’t intended to be a fix for Festool junkies, it just feels that way. I love this stuff.Ĭhamfer the edges of the panels and the tenons on the rails a little to help them slide into the stiles. I used the RO90 for this. I had ¼” VG Fir ply in stock but I wanted a ½” panel so I laminated two sheets together with spray adhesive. Once you have all your stiles and rails run, cut the panels. But I’ll admit I also made those cuts first because I was over eager to fondle the XL. I cut the mortise pockets in the rails first before cutting the tenons-so the rails would have square ends and better support for the Domino. Once the domino is added into the mix, those joints will tighten right up anyway. Having a little wiggle space here makes the glue up a lot easier. Here’s a tip, don’t fuss too much trying to make your stile and rail mortise and tenon joints super snug-you don’t want it sloppy, but you shouldn’t have to fight it. Tenoning each rail took less than two minutes each.Įxcuse me while I take another sip of the green koolaid here… umm my, that is delicious. This was one of those moments where the cost of a Festool product was immediately justified by the time it saved me to perform the task at hand. The MFT table and the router is almost too sweet for this use the precision and repeat-ability insure each rail is exactly the same, which is critical for building doors square. Dial in the cutter depth and then have at it. Pick your shoulder cut location and set up a stop on the MFT fence. First, set your router up on the guide rail. There’s high dollar machinery for this step too, but I found the MFT table to be a fantastic substitute, with my OF1000 router riding on the rail with a ¾” dado bit making a single pass per tenon side. Be sure to leave extra length for the tenons on each end. A few minutes with a sharp chisel and you have a nice clean bottom dado.
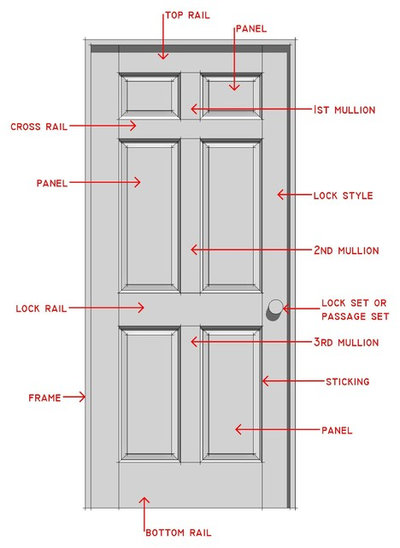
This is best done with a shaper, but I wanted to keep this job limited to tools most carpenters have access to, so I used the table saw. I do this before I cut the rails to exact length because it saves some time. Next we cut a dado into the stile and rail stock to accept the panels. I also inspect the lumber and will sometimes compromise the grain direction to bury a defect in the glue face. In fact, some of the grain actually turns at the end and runs the same direction as the piece it’s laminated to. I know that this photo doesn’t show that opposed grain as well as it might (see photo, right)-we got pretty lucky with vertical grain being…well…vertical. When laminating, it’s best to orient your lumber so the grain is opposed. Maybe this is why a lot of wood doors are made from fir.

The species is known for limited movement-great stability, and distinct hardness for a ‘softwood’. I try to select vertical grain materials, and Douglas Fir is a perfect choice.

Without further chatter let’s build some doors.įirst, to build doors from stock, you have to laminate your stiles and rails.
